
The inner radius wants to be a high-speed, low-pole-count motor while the outer radius wants to be a low-speed, high-pole-count motor.

The centrifugal forces also get large there. At the outer radius, the magnetic flux return path through the rotor backiron is quite long, and the magnetic pole faces are very broad, requiring the backiron to be quite thick. At the inner radius (near the axis of rotation), the surface speed of the rotor is quite low, as is the developed torque from magnetic pressure, so most of the power is generated by the material near the outer radius. The axial flux design scales somewhat awkwardly. At scale it may be better to just automate a high performance epoxied winding. PCBs are also not especially cheap at the large sizes, layer counts, and specialty copper weights demanded. Copper losses will be high because you typically can't get as good of a fill factor with PCB traces as with wound copper, so the phase resistance will be high, which impacts the efficiency They should be comparing against similar motors with rare earth magnets and integrated drives, which will tend to be very high efficiency and power-dense machines, rather than low cost induction motors.

It requires a high volume of rare earth magnets to get good performance.
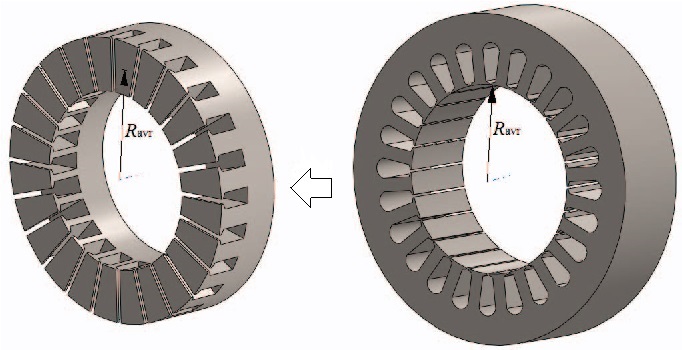
The article skips over the obvious downsides of this sort of motor design, which are:
